- 17 de junho de 2019
- Posted by: wcbm
- Category: Metodologia Lean
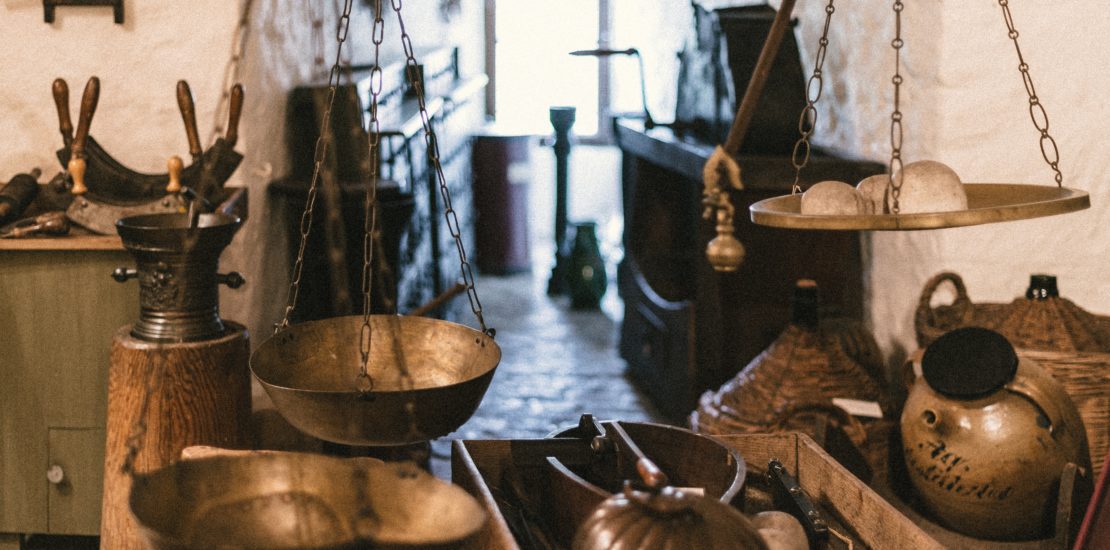
A eliminação das perdas, adotada pela maioria das empresas como o ponto central e muitas vezes único para o sucesso da manufatura lean, cobre apenas um terço das oportunidades de melhorias. Isso explica o porquê de escutarmos em algumas empresas que “o lean não funciona aqui”.
Nivelar ou balancear a carga de trabalho nos processos baseado na demanda do cliente é a primeira coisa a fazer antes de tentar implementar o sistema puxado no sistema como um todo. A responsabilidade é da área de gestão ou planejamento da produção.
O Problema:
Muitas empresas estão tentando se enquadrar no modelo de fazer o que o cliente quer e quando ele quer, o que está alinhado com os princípios lean; mas os clientes são imprevisíveis e os pedidos variam significativamente semana a semana e mês a mês.
Assim, ao cumprir com esta demanda extremamente variável, produz-se grandes quantidades em uma semana pagando horas extras e exigindo ao máximo as máquinas, e quase nada na semana seguinte, gerando ociosidade da mão de obra e baixa ocupação das máquinas.
E há outras consequências ao longo da cadeia de valor, porque devido à dúvida sobre o que, quando e quanto comprar dos fornecedores, a decisão normalmente é por aumentar o estoque baseado numa previsão do pedido máximo de cada cliente e produto.
Sem contar outras consequências negativas:
- Recursos dimensionados pelo “pico” histórico da demanda (mão de obra, máquinas e equipamentos, materiais), implicando em altos custos da operação com baixos índices de produtividade;
- Longos “lead time” de atendimento aos pedidos dos clientes;
- Alto nível de “stress” dos colaboradores e fornecedores;
- Baixo nível de qualidade;
A Solução:
A ideia é promover um processo de nivelamento no planejamento da produção para possibilitar uma operação mais enxuta e garantir aos clientes um atendimento melhor e com qualidade.
Isto quer dizer que nem sempre se produzirá por pedido recebido, pois isto pode gerar uma série de problemas nas operações originados por variações imprevisíveis na demanda, tanto no “mix” como no volume dos pedidos dos clientes.
O objetivo é “estabilizar” o sistema e estabelecer a “uniformidade”, gerando um fluxo de informações e materiais num regime o mais próximo do “laminar” e não “turbulento”, fazendo alguma analogia com a mecânica dos fluidos.
Assim, por exemplo numa demanda semanal de 20 produtos “A”, 15 produtos “B” e 5 produtos “C”, num sistema tradicional de programação da produção, provavelmente teríamos:
- segunda-feira: A A A A A A
- terça-feira: A A A A A A
- quarta-feira: A A A A A A
- quinta-feira: A A (troca de produto) B B B B B B B B B B
- sexta-feira: B B B B B (troca de produto) C C C C C
Este modelo de programação da produção gera “interrupções” geralmente demoradas seja pela troca de produtos, seja por outras paradas não programadas. Também gera momentos de alto e baixo “stress” em função da alta ou baixa dificuldade em produzir os diferentes produtos.
Trabalhando paralelamente para reduzir os tempos de troca de produto em nível suficiente para cumprir com o número de trocas de produtos previsto com base na demanda, reduzir as paradas não programadas e os problemas de qualidade, o novo modelo de programação focado no nivelamento seria:
- segunda-feira: A B A B A B A C
- terça-feira: A B A B A B A C
- quarta-feira: A B A B A B A C
- quinta-feira: A B A B A B A C
- sexta-feira: A B A B A B A C
Benefícios:
- flexibilidade para atender a demanda com redução de estoque;
- redução do risco de obsolescência;
- facilidade para balancear a mão de obra;
- facilidade para balancear a utilização de máquinas e equipamentos;
- melhoria na qualidade (fazer todos os produtos todos os dias);
- facilidade na reposição de materiais e componentes;
- demanda balanceada para os processos internos e para a cadeia de suprimentos;
- menor desgaste “físico e mental” dos colaboradores e fornecedores.
Mas, para que este cenário seja exequível, é necessário que também haja mudanças de paradigmas por toda a organização. Alguns exemplos:
- Foco na melhoria dos processos como potencial tema de alavancagem dos resultados operacionais. Porque se um processo não está bem, coloque você quem for para operar este processo, ele vai falhar.
- O operador deve ser considerado como um “cirurgião” (explicação: “O cirurgião opera? Sim. O operador opera? Sim. Portanto, o operador é um cirurgião”. E você não vê um cirurgião “caminhando” ou “esperando” por aquilo que necessita para operar. Segundos podem fazer a diferença entre salvar ou não o paciente “aberto”, correto?). Lembre-se “operador-cirurgião” caminhando, não opera. Não operando, não produz. Não produzindo, não entrega o que o cliente necessita. Simples assim!
- A padronização de componentes do produto e processos flexíveis e confiáveis (“robustos”). As engenharias de produto e processo têm fundamental importância na busca pela excelência operacional. A padronização de partes e componentes associada à processos flexíveis com trocas rápidas de produtos e confiáveis no sentido de robustez, são fatores chaves para se alcançar a Excelência Operacional.
A tentação de implementar “modularmente” as soluções exemplificadas pode levar a uma situação insatisfatória quanto aos resultados financeiros e operacionais. A ideia é promover uma implementação metódica e efetiva, o que inicialmente pode requerer algum suporte externo de especialistas no assunto.
Os profissionais da WCBM Consultoria Empresarial Ltda. possuem mais de 20 anos de experiência como executivos na indústria, seguidos de 15 anos em consultoria, e já ultrapassaram a marca de 1.000 projetos de base lean com foco em Qualidade, Entrega, Custo, tanto em nível estratégico como tático, implementados em mais de 200 empresas na América do Sul, América Central, América do Norte, Europa e África do Sul.
Caso queira discutir algum tema deste artigo, fale conosco sem compromisso.
Washington Kusabara
Sócio Diretor e Consultor
Photo by Roman Kraft on Unsplash